
Over the past 20 years, the garment industry has undergone dramatic transformations. From relocating production lines to Africa instead of Asia, to the introduction of digital garment printing and the use of automated machinery,
. Most of these changes enable the industry to make cheaper, prettier and more garments in a faster way.

The rise of Fast Fashion encourages consumers to purchase more garments than ever before. This trend has not only expanded our wardrobes beyond what previous generations experienced, but it has also positioned the garment industry as the second largest global polluter.
There is a growing consensus that the garment industry must adopt more sustainable technologies. This includes initiatives like growing cotton with fewer pesticides, minimizing fabric waste, and improving water reuse systems. However, these advancements often require significant investment and new technologies.
​
Softag, a young and energetic enterprise, leads an evolution for fashion sustainability. Start from a part as small as our thumbs - Tagless Label.
Before diving into the details of Tagless labels, let’s compare them with traditional Heat Transfer labels. The primary advantage of Tagless label printing is the elimination of transfer mediums, such as paper or plastic films used in Heat Transfer labels.

Tagless Label Printing

Heat Transfer Label
It is estimated that producing one A4 sheet of paper consumes 20 liters of fresh water. By opting for Tagless labels, we can save approximately 500 ml of fresh water for each label printed.
​
Additionally, for every 250,000 Tagless labels produced, we save a tree that would otherwise be cut down for paper.
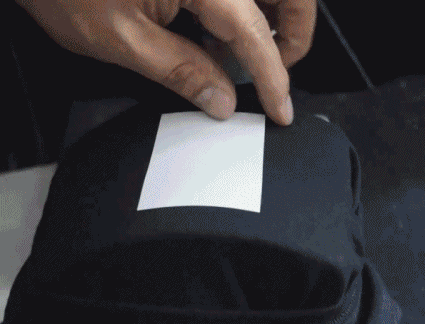
A single can of Delta ink can print up to 12,000 labels, requiring minimal logistical effort and storage space.
Unlike Heat Transfer labels, Tagless label printing does not involve any heat during the application process. This method consumes only one-tenth of the energy used by heat transfer machines, making it significantly more energy-efficient.


While garment labeling might seem like a small aspect of the industry, every garment carries at least one label. Implementing Tagless label printing represents a substantial step toward fashion sustainability, engaging multiple stakeholders, including fashion brands, garment factories, workers, and consumers, in the effort to protect our planet.
A garment with Tagless label, at the same time , also repays these stakeholder. Brands not only improves consumers' wearing experience, applying Tagless express a strong message of maintaining business ethic.
Apart from feeling comfortable when wearing the garment with Tagless label, consumers no longer spend a minute to remove the annoying woven labels.
Unlike many sustainable initiatives, the investment required for Tagless production is relatively minor. Factories that adopt Tagless production lines can often recoup their investment within just a few months.